How to Cure Concrete: The Only Guide You'll Need
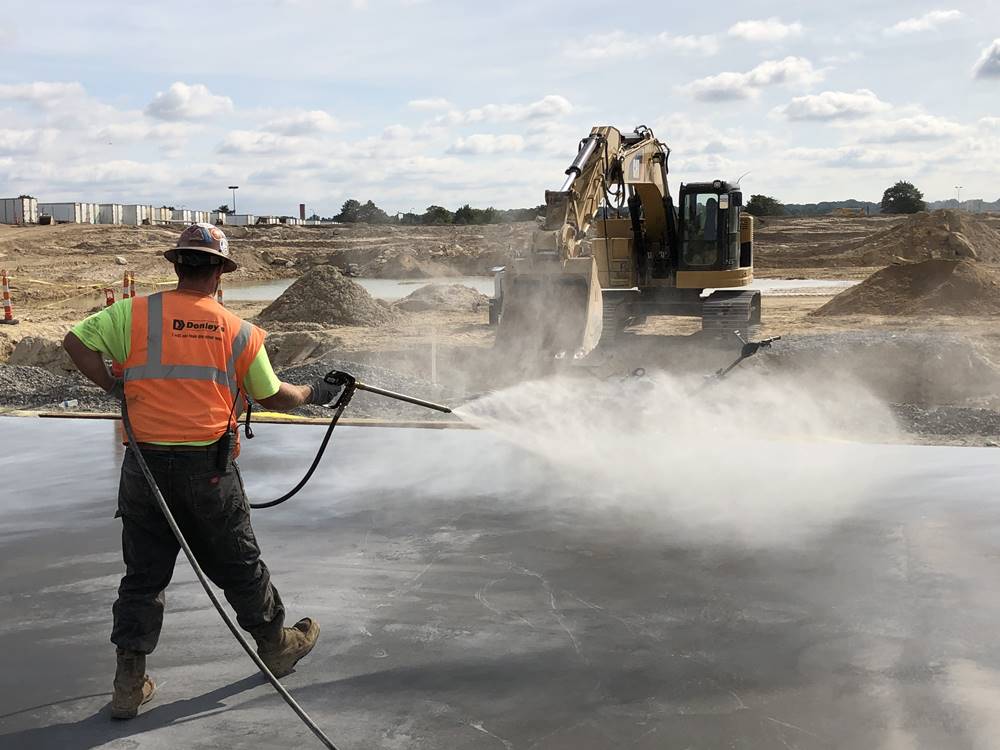

Brian Jeffries
Brian Jeffries, a seasoned BPA Advisor. Brian is dedicated to sharing his wealth of knowledge on construction projects and materials. With a focus on architecture and building envelopes, Brian contributes valuable insights that shape the discourse around innovative construction practices and materials.
Although you may believe that concrete is one of the most appealing and lasting building materials available, did you realize that the things you do after pouring have as much of an impact on the material's strength as the mixing procedure? In actuality, it takes roughly 28 days for the chemical reaction between the cement and the water to completely bind sand and gravel together to produce concrete. You want to preserve moisture in the concrete throughout this critical time. Otherwise, the finished product will get stressed and crack — especially if water evaporates too quickly from the surface, which can happen easily outside and in direct sunlight.
The primary goal of curing is to regulate the new concrete's temperature and moisture content over the first few days. You can improve the structural integrity of the concrete while also making it more resistant to future breaking by paying closer attention to the concrete mix during this time rather than leaving it alone once it has been poured.
What Does Curing Mean?
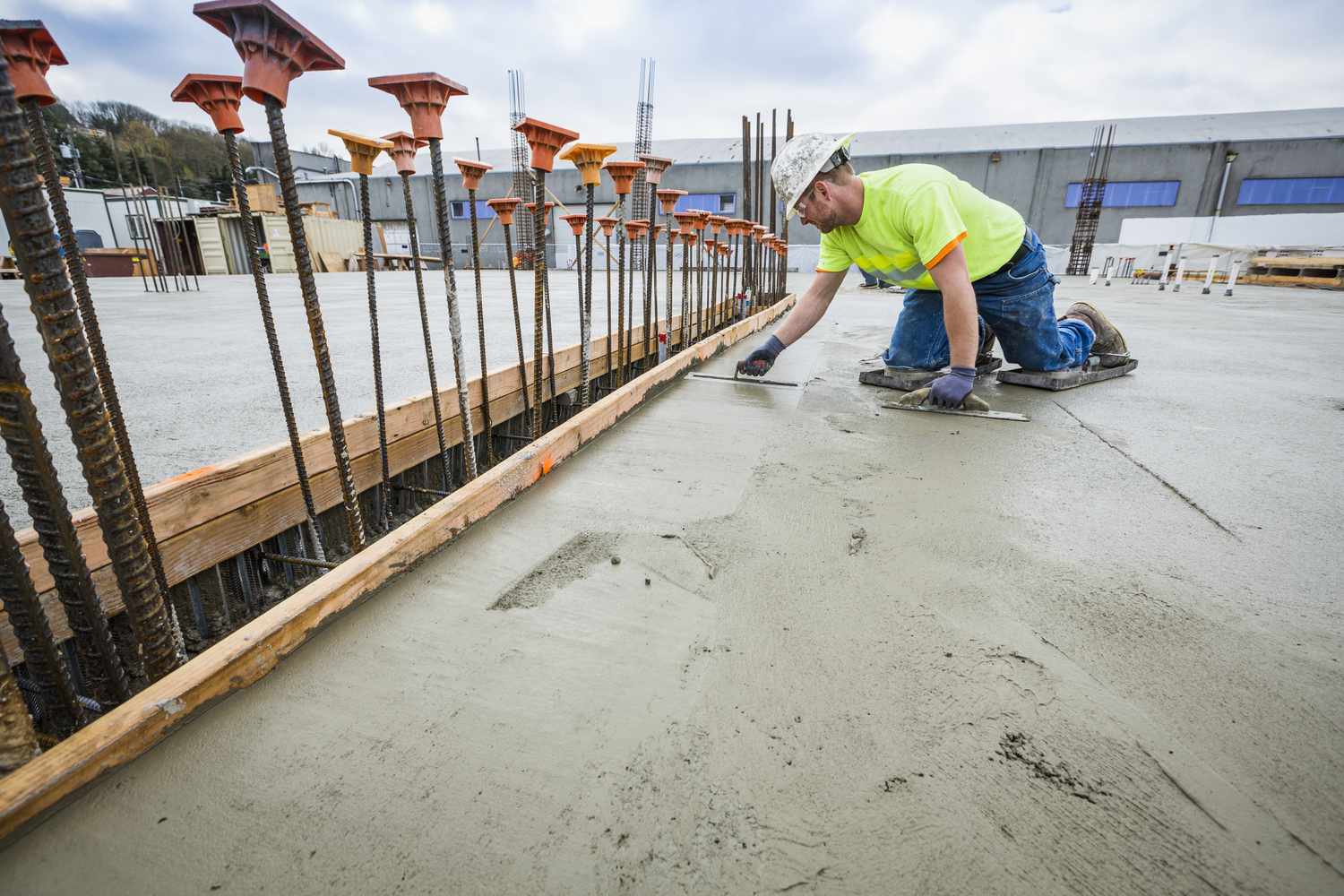
Image Source: liveabout.com
Curing is the process of giving concrete the right amount of moisture, heat, and time to develop the correct qualities for its intended application. In order to achieve this, the concrete should be kept at a temperature of at least 50 degrees Fahrenheit, with a relative humidity of at least 80 percent, for a period of time that generally ranges from three to fourteen days, depending on the application. The final qualities of the concrete mixture will be reached if these recommendations are appropriately carried out.
Curing concrete is not the same thing as drying. Concrete drying creates the ideal environment for the concrete to reach the proper moisture level for its intended application. For the application of moisture-sensitive floor finishes like vinyl composition tile, linoleum, wood flooring, and non-breathable coatings like epoxy, the moisture state of a concrete slab is crucial. To ensure the proper application of the flooring materials, a typical value given for relative humidity may be less than 75 to 80 percent.
Is Curing Concrete Necessary?
Every concrete structure needs proper curing to gain full strength. Curing is usually done for 28 days because 99% of strength is obtained during this period. Another reason for curing is that water loss from the inside of concrete leads to pores inside the structure, which causes a reduction in strength. Cracks can develop, which reduces the load-transferring area.
How to Cure Concrete: The Process
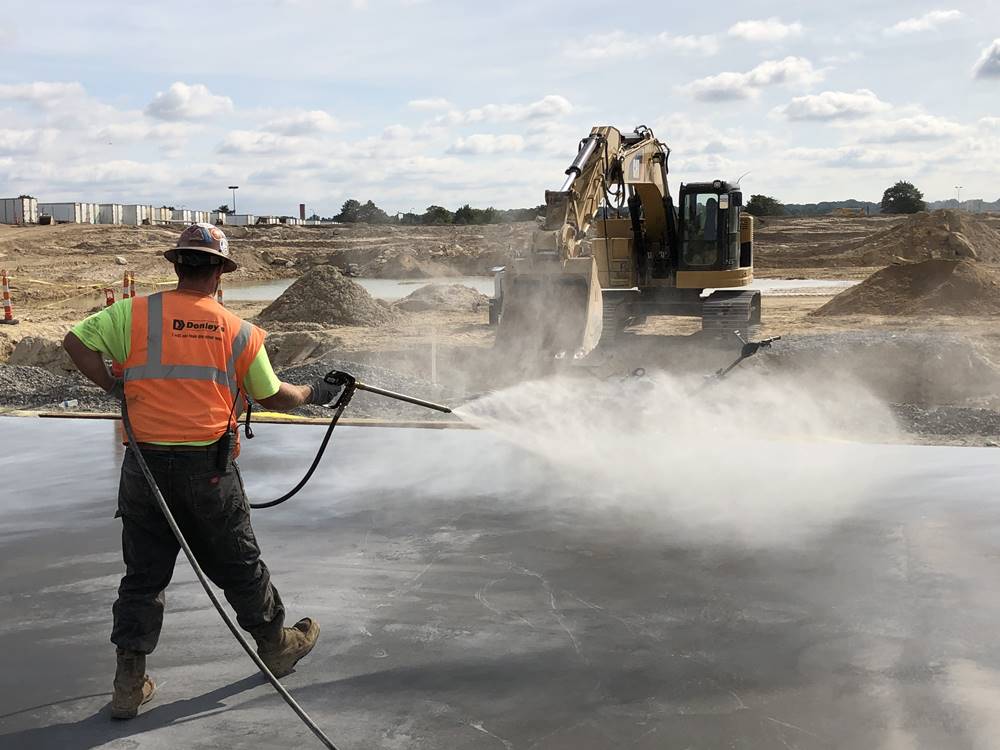
Image Source: concretedecor.net
There are a few ways that concrete can be cured. Traditionally, water curing was the preferred method.
When water is used to cure concrete, it will form a coating that will keep moisture from evaporating from the surface for a long time, preventing excessive moisture loss. The concrete will eventually begin the chemical process that will cause it to harden over some time.
Water Curing Techniques
Immersion: When curing concrete test specimens, immersion curing is typically used during the testing of concrete.
Ponding: Used to cure flat surfaces in controlled environments or where water can easily be kept on top of the concrete slab. The slab is surrounded by sand or dirt dikes, and a layer of water is kept on top of the slab.
Fogging: When the temperature is above freezing and the humidity is low, fogging or misting is used. By repeatedly spraying a fine mist of water across the curing concrete to keep it moist, fogging increases the humidity above it.
Wet Covering: After the concrete has adequately set and the water covering won't harm the concrete's surface, it is cured using a wet covering. Sand, burlap, canvas, or straw are typical coverings that are maintained consistently damp throughout the curing process.
You can also use plastic sheeting to cure concrete.
The most practical and effective approach to cure concrete in the modern construction industry is with a membrane or plastic sheet. Water curing may not always be the best choice as water may not be available. Plus, if water curing is done incorrectly, it may damage the strength or surface finish of the concrete.
Plastic Curing Techniques
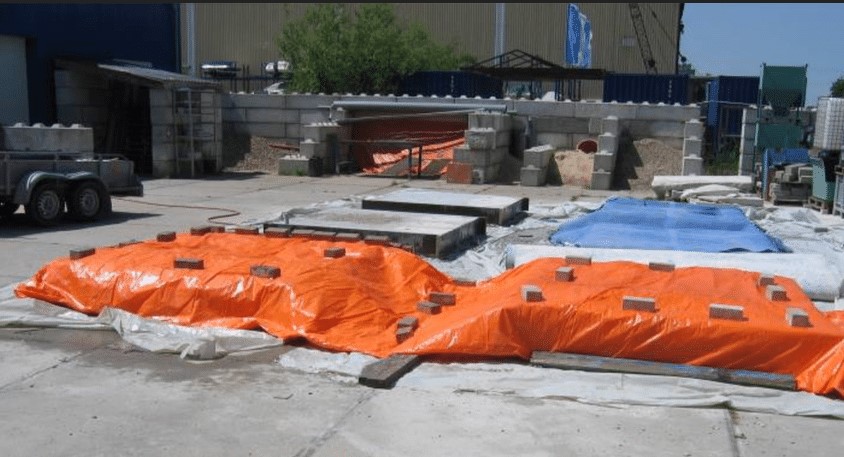
Image Credit: researchgate.net
Plastic Sheeting: To cure concrete with plastic sheeting, it is necessary to immediately cover all exposed concrete without compromising the concrete finish. Plastic sheeting over flat surfaces like slabs or pavements should extend beyond the slab's edges by a distance that is at least twice as long as the slab's thickness.
Membrane-Forming Curing Compounds: Curing compounds are chemical substances that are often sprayed directly onto the surface of concrete and let to dry. The substance creates an impermeable film that slows the concrete's moisture loss.
Another way to cure concrete involves a spray-on compound.
Utilizing a curing agent is currently the method of choice for curing concrete. Once the concrete has cured but still contains water, the chemical needs to be applied. The curing compound might not yield the greatest results if you wait until all the water has evaporated. Use the proper sprayer to ensure that the compound is administered in the right quantity and is covered uniformly.
Prosoco makes a popular curing and densifying compound called DensiKure. In a single application, DensiKure densifies and cures freshly laid, slick, steel-trowel-finished concrete. Pump-up sprayers make applying this mixture of a high-performance hardener and densifier simple, which dries in about 60 minutes.
Tips and Tricks
Mind the temperature.
The optimal time to pour concrete is when it's anticipated that the temperature will stay over 50 for five to seven days, but things can go wrong if a sudden cold front moves in. When that occurs, maintaining the concrete's moisture content becomes less important than maintaining its temperature so that the chemical hardening process doesn't get halted. Concrete's chemical reaction slows at 50 degrees Fahrenheit and stops entirely at 45 degrees. Therefore it will become dormant and stop strengthening. Concrete insulating blankets should be placed over fresh concrete as the weather becomes chilly. After the first two to three days, fresh concrete should be robust enough to withstand the cold without risk of damage.
Expert Insight: "Tim Gomez of El Paso Precision Concrete Contractors underscores the significance of maintaining a consistent temperature during the concrete curing process. He advises using thermal blankets or insulating covers, especially in fluctuating outdoor temperatures, to keep the concrete at an optimal temperature range. According to Gomez, this method helps to prevent thermal cracking and ensures uniform strength development throughout the structure."
Don't stain or paint it too soon.
Remaining moisture or the concrete's shifting chemical composition may adversely influence any paint or stain applied while it is still setting. All of the water must be consumed within a month for the hydration procedure to be complete. Applying paint with a brush while moisture is still rising to the top puts pressure beneath the paint barrier, which can cause the paint to peel or the bond to dissolve. Because of this, the paint might not adhere as effectively, and stained concrete's final color and appearance might also be impacted. Wait until the 28-day period is over before applying paint or stain for the greatest results.
Give it time.
Although concrete will harden shortly after being poured, the first four weeks are when it is still vulnerable to harm from weight. When using a freshly poured sidewalk or slab, wait at least 24 hours before allowing people or their pets to use it, and wait at least 10 days before driving a car on a freshly installed driveway. Regular passenger cars can then be driven on the concrete, and once the concrete has had around 28 days to acquire its full strength, huge trucks or RVs can be rolled into the driveway.
Get Smarter About Building Products
Join 50,000+ subscribers and get our 3 min daily newsletter on what matters in the building materials industry.
You might like this
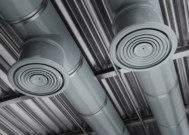

Solving Ventilation Challenges: Metal Deck Profiles and Back Draft Dampers as Key Solutions
When it comes to building design and construction, ventilation is a critical factor that often presents significant challenges. Proper ventilation is essential for maintaining indoor air quality, controlling temperature, and ensuring occupant comfort and safety. In this article, we will explore how metal deck profiles and back draft dampers are key solutions for addressing ventilation […]
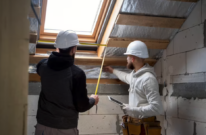

The Ultimate Guide to Home Insulation
When it comes to creating a comfortable and energy-efficient home, insulation plays a pivotal role. Proper insulation helps regulate indoor temperatures, reduces energy consumption, and enhances overall comfort. In this comprehensive guide, we’ll explore various aspects of home insulation, including the best types of insulation for different areas of your home and key considerations for […]
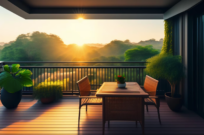

The Best Hidden Deck Fasteners: Concealed Elegance and Lasting Stability
Decks, those quintessential outdoor havens, serve as extensions of our living spaces, inviting us to bask in the open air. But what if we could take this experience to the next level? Enter concealed deck fasteners, the unsung heroes that elevate your deck’s appearance and structural integrity, all while keeping their existence a secret. In […]