How Much Does it Cost to Build a 50,000 Square Foot Warehouse
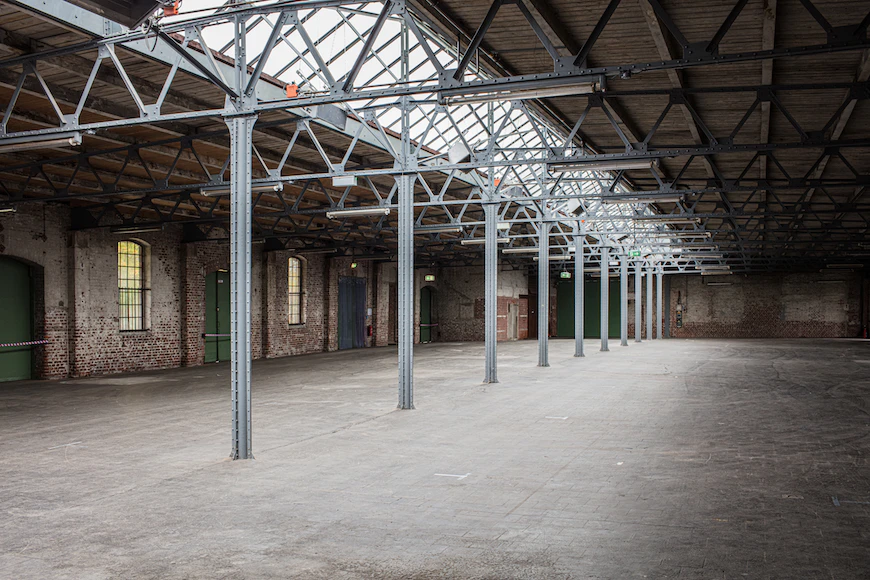

Brian Jeffries
Brian Jeffries, a seasoned BPA Advisor. Brian is dedicated to sharing his wealth of knowledge on construction projects and materials. With a focus on architecture and building envelopes, Brian contributes valuable insights that shape the discourse around innovative construction practices and materials.
From e-commerce fulfillment centers to sprawling self storage facilities, the demand for industrial space has increased by 24% since 2010. And with not enough buildings to accommodate this demand, developers will be looking for every opportunity to break ground on warehousing projects in 2023. But how much does it cost to build a 50,000 square foot warehouse?
As a general estimate, it can cost as little as $500,000 to as much as $2,000,000 to build a 50,000 square foot warehouse.
While these figures provide a solid starting point for a warehouse project, there are a number of factors that can impact the final quote. Keep reading for a complete breakdown of warehouse construction costs in 2023!
Cost Estimates for a 50,000 Square Foot Warehouse
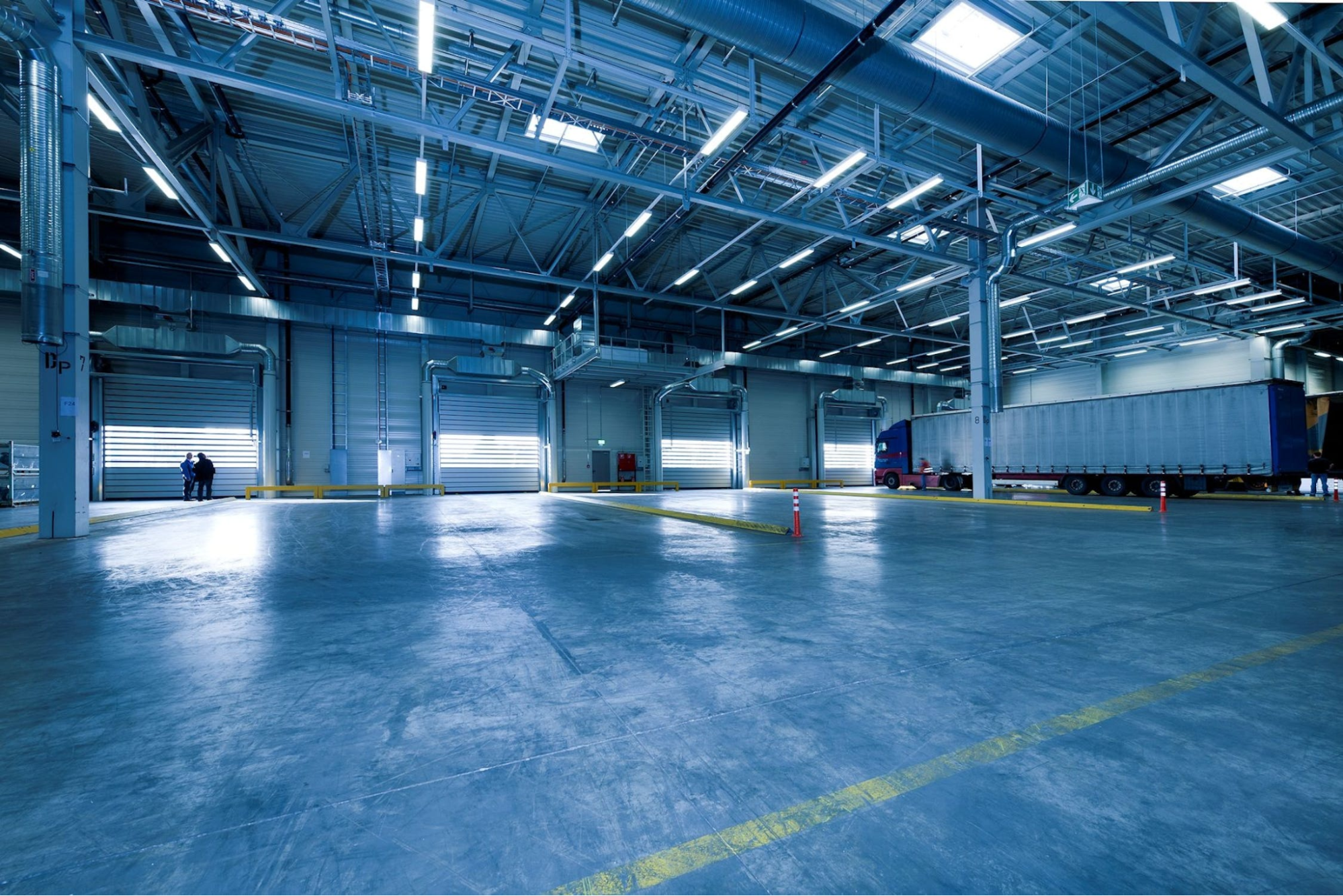
There are several different techniques in warehouse construction, each with a different average price point:
- Stud frame construction - between $20 and $40 per square foot
- Tilt-up construction - between $25 and $40 per square foot
- Steel frame construction - between $10 and $20 per square foot
Stud frame construction is the most traditional form of building framing. It uses a series of vertical studs, usually in the form of 2X4 or 2X6 boards, spaced 16 to 24 inches apart around an extensive concrete foundation. It is the most labor intensive form of framing, and due to its high fire susceptibility and poor weather resistance, it is falling out of favor as a commercial warehouse framing method.
Tilt-up construction is gaining popularity due to its utility in creating energy efficient buildings. Using this construction type, insulated panels are set with concrete on the construction site and “tilted up” to create the warehouse frame. The concrete walls create an air and moisture resistant barrier, with the insulative core creating a decoupling effect that leads to elite R-value in the building. Tilt up construction can be performed with smaller crews than stud frame construction, leading to some cost savings.
Steel frame construction is the most popular method for creating modern warehouses. Not only is steel a durable and long-lasting material, but it allows for greater height and fewer interior support beams than other framing materials. Thanks to their outstanding strength, structural steel panels can be spaced as much as 30 feet on center without requiring an anchor. This “clear span” interior gives the facility much greater flexibility for maneuvering vehicles and adding racks. Many steel buildings--sometimes referred to as pre-engineered metal buildings (PEMB)--can be partially fabricated off site, allowing for erection in a fraction of the time at the final location. Finally, steel frame construction generally requires less elaborate foundations for support than the other construction types.
Factors That Influence Cost of a Warehouse
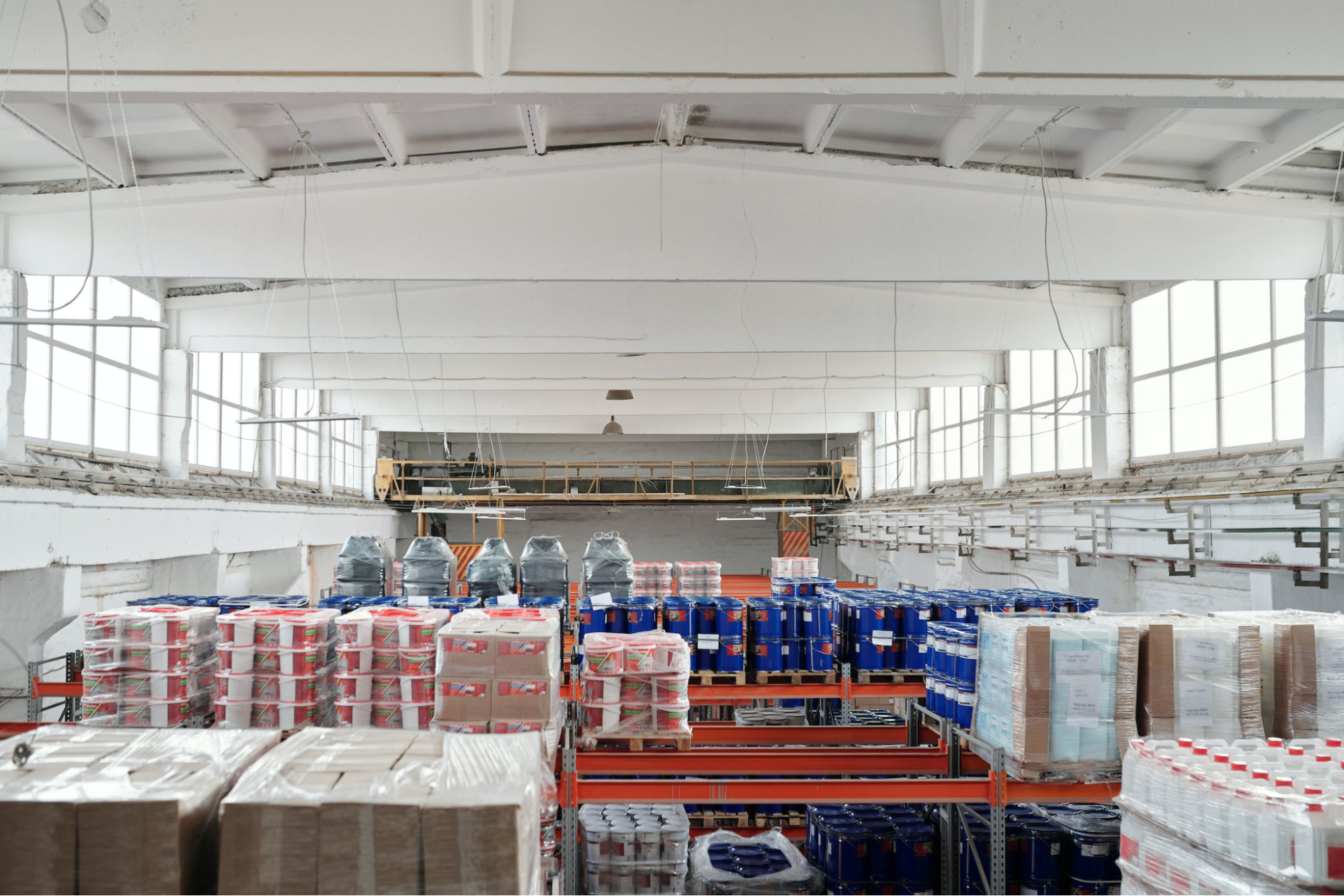
While the figures listed above are a great starting point for estimating the cost of a 50,000 foot warehouse, there are myriad factors that could make the final price tag significantly higher or lower than these figures. Some points to keep in mind include:
- What will the warehouse be used for? Simple storage facilities will be cheaper to build than more dynamic fulfillment centers that require elite warehouse insulation and climate controls to protect employees and product
- What is the market like for building materials? The past couple of years have seen unprecedented rises in the cost of most construction materials. However, remember that the market is inherently volatile due to supply chain challenges and opportunities, so expect to see seasonal changes in price or materials
- Where is the building located? Generally, warehouses are more expensive to build in coastal regions than they are in land-locked areas. Regardless, if there are any special weather or climate considerations required in a specific area to ensure that the warehouse passes code, be prepared to pay a little extra
- What’s the state of the labor market? Like the building materials market, the labor market can be quite volatile. Given the shortage of construction workers across the country, be prepared to pay a premium for qualified professionals and pay a little extra to train other workers to get the project done right and on time
When all of the various factors are taken into consideration, don’t be surprised if the total project estimate ends up being as much as 30% higher or lower than expected.
Long-Terms Costs of a 50,000 Square Foot Warehouse
As in all walks of life, there is considerable interest in the realm of sustainable warehousing. Many companies are willing to pay a bit more upfront to help save money and limit resource consumption over time. Some ongoing costs for a 50,000 foot warehouse include:
- Utilities - facilities with better metal building ventilation, insulation and natural lighting will help keep utility costs under control
- Maintenance - buildings that require less cleaning, painting, and renovation will be more affordable in the long run
- Insurance - warehouses better equipped to withstand wildfires and other forms of natural disaster will pay lower insurance premiums
All in all, it is important to remember that the most affordable warehouse upfront will not necessarily be the most cost-effective solution when looking back 30 years later.
Choose the Right Materials and Keep Warehouse Construction Costs Under Control
For most applications, it will cost between $10 and $40 per square foot to build a warehouse. For a 50,000 square foot facility, the total project will end up being between $500,000 and $2,000,000. Although these are great ballpark figures, there are many variable costs that could cause the final price tag to go up or down, and the lifetime costs of ownership should also be factored into the equation.
Get Smarter About Building Products
Join 50,000+ subscribers and get our 3 min daily newsletter on what matters in the building materials industry.
You might like this
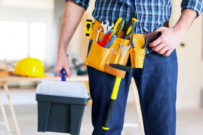

Toolbox Treasures: Exploring Must-Have Construction Components
Constructing a building, whether it’s a towering skyscraper or a cozy home, is a complex puzzle that requires a skilled hand and the right set of tools. In the world of construction, having the right components in your toolbox can make all the difference. From sealers that protect against the elements to essential hardware that […]
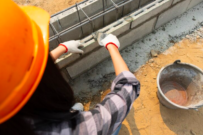

7 Advantages of Insulated Concrete Forms (ICFs) in Sustainable Construction
In the ever-evolving landscape of construction, the emphasis on sustainable building practices has become paramount. Among the innovative solutions revolutionizing the industry, Insulated Concrete Forms (ICFs) stand out as a versatile and eco-friendly alternative, offering a myriad of advantages in the realm of sustainable construction. 1. Energy Efficiency at its Core At the heart of […]
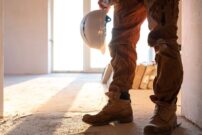

Clean & Safe: Mastering Jobsite Cleanup for a Secure Workplace
A well-organized and clean job site is not just a matter of appearances- it plays a crucial role of ensuring safety and security to any jobsite. A tidy space reduces the chances of accidents, promotes better focus, and boosts employee morale. Plus, it sends a clear message that the organization values the health and safety […]